Supply Chain Planner
8041
Posted: 13/11/2024
- Competitive
- Germany
- Semiconductor
- Permanent
Supply Chain Specialist - Planning
This position is responsible for developing a master production plan that satisfies customer demand while maintaining minimal effective inventory. Collaboration with Sales, Customer Service, Purchasing, and Management is crucial for achieving business goals through the Sales, Inventory, and Operations Planning (SIOP) process. The role also involves participating in continuous improvement initiatives to enhance efficiency and standardize processes across various sites within the organization.
Why This Role is Attractive
This role offers a fantastic opportunity for career growth in supply chain management, with hands-on experience in material planning and forecasting. The position also provides real potential for career advancement toward future management roles.
Key Responsibilities
- Develop and maintain demand forecasts for assigned product lines, collaborating with Sales, Marketing, and other stakeholders in an ERP environment to ensure data accuracy and alignment with customer and revenue goals.
- Schedule sales orders, providing accurate ship dates to the Customer Service team, and work to improve ship dates to meet customer requirements.
- Generate production orders and work closely with stockroom and production teams to ensure timely customer shipments and clear communication regarding ship dates.
- Collaborate with Manufacturing, Engineering, and Purchasing teams to ensure customer orders are fulfilled on time, and cross-train in relevant areas.
- Partner with Procurement to identify and prioritize critical supply components.
- Track and manage inventory levels for assigned products, addressing exceptions such as shortages and quality issues.
- Participate in revenue tracking, highlighting potential upsides and downsides to maximize revenue and customer satisfaction.
- Manage change orders and Corrective/Preventive Actions (CAPA) in collaboration with cross-functional teams, and work with colleagues across sites to standardize processes and drive improvements.
- Lead or participate in continuous improvement projects within the supply chain.
- Participate in internal audits and ensure compliance with relevant laws, regulations, and corporate policies.
Required Qualifications and Skills
- Diploma/Degree qualification and relevant training in planning or MRP; APICS certification or equivalent experience preferred.
- Strong knowledge of supply chain processes, including demand forecasting, manufacturing planning, and replenishment processes.
- Strategic thinking and strong analytical skills for managing complex data.
- Proficiency in Microsoft Office, with advanced skills in Excel.
- Effective negotiation and communication skills, with the ability to influence at all levels.
- Experience managing complex priorities in a team-oriented, cross-functional environment.
Preferred Qualifications
- Six years of experience in supply chain and inventory management within a manufacturing or logistics setting, ideally with a multi-level BOM structure.
- Familiarity with import/export requirements.
- Proficiency in MRP systems for multi-level BOM structures.
- Experience interfacing with senior management for reporting purposes.
- Self-starter with a proven track record in delivering results.
- Knowledge of ERP systems (e.g., Axapta, Microsoft Dynamics, SAP, or Oracle).
- Familiarity with Lean Supply Chain principles and a history of contributing to Lean initiatives.
- Proficiency in both German and English.
Competencies
- Goal-oriented and results-driven approach.
- Strong analytical skills, with the ability to quickly assimilate data and assess situations.
- Excellent communication skills across all levels of the business.
- Adaptable, creative, and able to handle new challenges effectively.
This position is responsible for developing a master production plan that satisfies customer demand while maintaining minimal effective inventory. Collaboration with Sales, Customer Service, Purchasing, and Management is crucial for achieving business goals through the Sales, Inventory, and Operations Planning (SIOP) process. The role also involves participating in continuous improvement initiatives to enhance efficiency and standardize processes across various sites within the organization.
Why This Role is Attractive
This role offers a fantastic opportunity for career growth in supply chain management, with hands-on experience in material planning and forecasting. The position also provides real potential for career advancement toward future management roles.
Key Responsibilities
- Develop and maintain demand forecasts for assigned product lines, collaborating with Sales, Marketing, and other stakeholders in an ERP environment to ensure data accuracy and alignment with customer and revenue goals.
- Schedule sales orders, providing accurate ship dates to the Customer Service team, and work to improve ship dates to meet customer requirements.
- Generate production orders and work closely with stockroom and production teams to ensure timely customer shipments and clear communication regarding ship dates.
- Collaborate with Manufacturing, Engineering, and Purchasing teams to ensure customer orders are fulfilled on time, and cross-train in relevant areas.
- Partner with Procurement to identify and prioritize critical supply components.
- Track and manage inventory levels for assigned products, addressing exceptions such as shortages and quality issues.
- Participate in revenue tracking, highlighting potential upsides and downsides to maximize revenue and customer satisfaction.
- Manage change orders and Corrective/Preventive Actions (CAPA) in collaboration with cross-functional teams, and work with colleagues across sites to standardize processes and drive improvements.
- Lead or participate in continuous improvement projects within the supply chain.
- Participate in internal audits and ensure compliance with relevant laws, regulations, and corporate policies.
Required Qualifications and Skills
- Diploma/Degree qualification and relevant training in planning or MRP; APICS certification or equivalent experience preferred.
- Strong knowledge of supply chain processes, including demand forecasting, manufacturing planning, and replenishment processes.
- Strategic thinking and strong analytical skills for managing complex data.
- Proficiency in Microsoft Office, with advanced skills in Excel.
- Effective negotiation and communication skills, with the ability to influence at all levels.
- Experience managing complex priorities in a team-oriented, cross-functional environment.
Preferred Qualifications
- Six years of experience in supply chain and inventory management within a manufacturing or logistics setting, ideally with a multi-level BOM structure.
- Familiarity with import/export requirements.
- Proficiency in MRP systems for multi-level BOM structures.
- Experience interfacing with senior management for reporting purposes.
- Self-starter with a proven track record in delivering results.
- Knowledge of ERP systems (e.g., Axapta, Microsoft Dynamics, SAP, or Oracle).
- Familiarity with Lean Supply Chain principles and a history of contributing to Lean initiatives.
- Proficiency in both German and English.
Competencies
- Goal-oriented and results-driven approach.
- Strong analytical skills, with the ability to quickly assimilate data and assess situations.
- Excellent communication skills across all levels of the business.
- Adaptable, creative, and able to handle new challenges effectively.
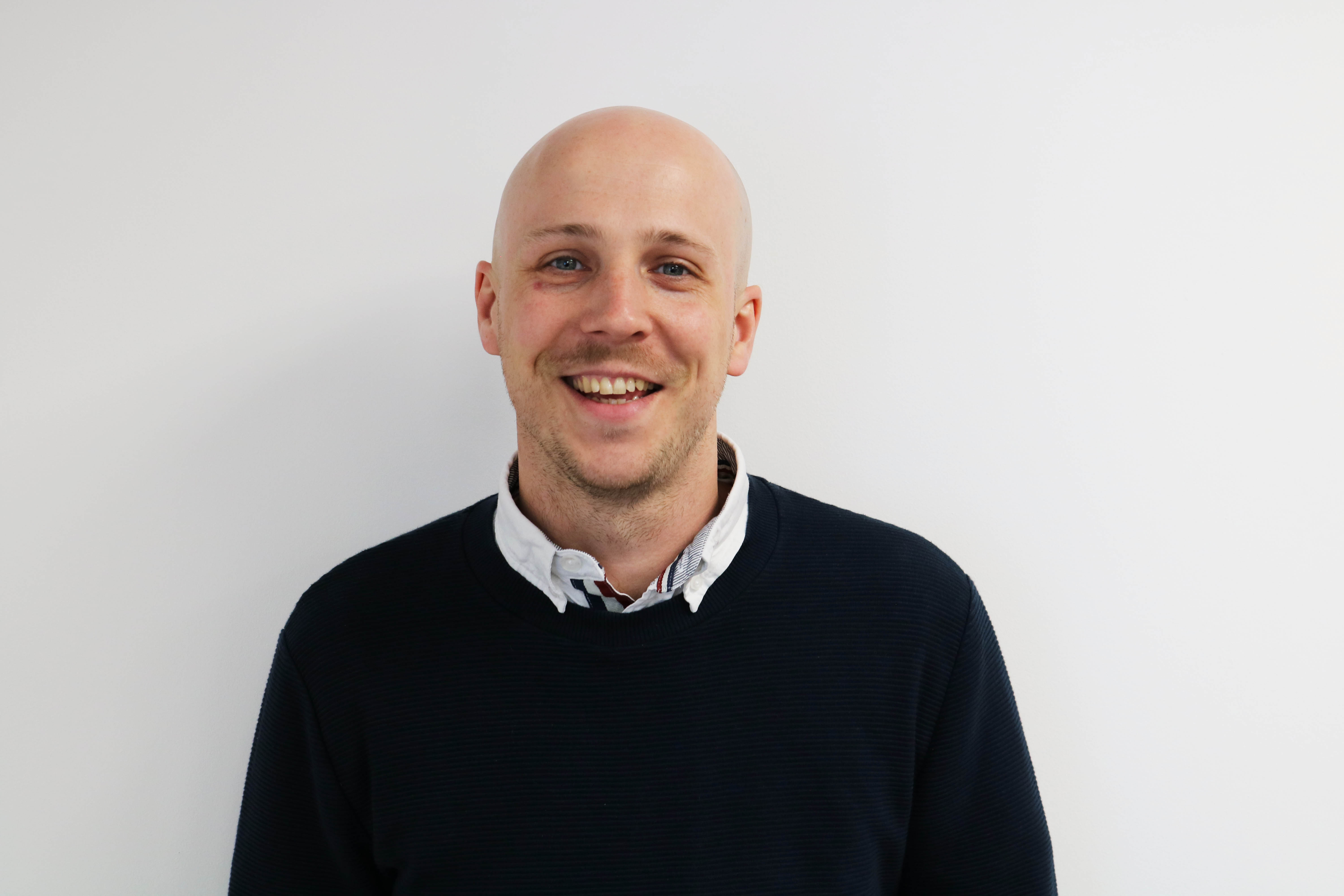
James Dees
Principal Account Manager